为了使塑件在推出过程中不发生变形和损坏,设计模具时应仔细进行塑件对模具包紧力和粘附力大小的分析与计算,合理的选择推出的方式、推出的位置、推出零件的数量和推出面积等。对于外观质量要求较高的塑件,塑件的外部表面尽量不选作推出位置,即推出塑件的位置尽量设在塑件内部。对于塑件内外表面均不允许存在推出痕迹时,应改变推出机构的形式或设置专为推出使用的工艺塑料块,在推出后再将工艺塑料块与塑件分离。
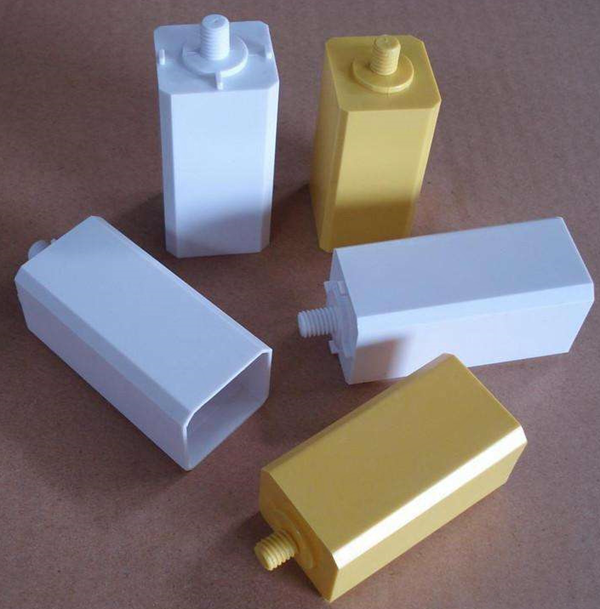
设计推出结构时,应考虑合模时推出机构的复位,在斜导杆和斜导柱侧向抽芯及其他特殊的情况下,还应考虑推出机构的先复位问题等。推出机构在推出与复位的过程中,结构应尽量简单, 动作可靠、灵活,制造容易。塑件注塑成型后,塑件在模内冷却定形,由于体积收缩,对型芯产生包紧力,当其从模具中推出时,就必须先克服因包紧力而产生的摩擦力。
对底部无孔的筒、壳类塑料制件,脱模推出时还要克服大气压力。型芯的成型端部,一般均要设计脱模斜度。另外还必须明白,塑件刚开始脱模时,所需的脱模力最大,其后,推出力的作用仅仅是为了克服推出机构移动的摩擦力。脱模力的大小随着塑件包络型芯的面积增加而增大,随着脱模斜度增大而减小,同时也和塑料与钢之间的摩擦系数有关。
推出机构按照模具的结构特征可分为一次推出机构、定模推出机构,二次推出机构、浇注系统推出机构、带螺纹的推出机构等。由于推出机构的动作是通过注塑机的动模一侧的顶杆或液压缸来却动的,所以,在一般情况下,塑料加工模具的推出机构设在动模一侧。正是由于这种原因,在考虑塑件在模具中的位置和分型面的选择时,应尽量能使模具分型后塑件留在动模一侧,这就要求动模部分所设置的型芯被塑件包络的侧面积之和要比定模部分的多。
影响脱模力的因素很多,型芯的表面粗糙度、成型的工艺条件、大气压力及推出机构本身在推出运动时的摩擦阻力等都会影响脱模力的大小。另外,同一模腔中在几个凸起或几个凹下之间由于相对位置引起塑料收缩应力造成的脱模力以及塑件与模具型腔之间的粘附力在脱模力计算过程中有时也不可忽略。
更多精彩文章:垫块、定动模座板的设计,直接点击。
http://www.suliaovip.com/service/news/news/2017/0518/259.html
南通锦程塑业官方网站:http://www.zhusuoem.com/
更多精彩文章 ,立即搜索:锦程注塑加工